Menatek’s Specialized Expertise in Heavy to Light Military Vehicles
Menatek Defense Technologies has 50 years of specialized know-how on manufacturing main systems and subsystems of heavy to light military vehicles to provide manufacturing, testing, and supplying services. We offer MRO, modernization, and localization solutions, and has delivered over 150,000 components to more than 35 countries. We produce high-tech components using over 550 manufacturing processes, such as Casting, CNC Machining & Grinding, Gear Manufacturing, Forging, and Cold Forming.
If we have to mention about these processes shortly;
Casting is a manufacturing process in which a liquid material is poured into a mold, which shapes the material as it cools and solidifies. Menatek has several types of casting capabilities, including sand casting, investment casting, shell mold casting, gravity die casting, and die casting. Sand casting is a relatively inexpensive process and is commonly used to create large, complex parts of Menatek’s products, while investment casting is a precise process that is commonly used to create small, high-precision parts. On the other hand, shell mold casting is a faster and more economical process than investment casting, but it is not suitable for casting very small or intricate parts. Gravity die casting is a fast process that is suitable for high-volume production, while die casting is a fast and efficient process that is commonly used to produce small, precise parts.

CNC machining is a highly precise method of manufacturing that can produce parts with tight tolerances and fine details. In addition, grinding is a machining process that involves the use of abrasive particles to remove material from a workpiece. Ultra-precise CNC machining and grinding refers to the use of advanced CNC equipment and techniques to produce parts with extremely high levels of precision and accuracy. This may involve using high-precision measuring instruments to ensure that parts are fabricated to extremely tight tolerances, as well as using specialized grinding tools and techniques to achieve a very smooth, precise finish on the surface of the part. Ultra-precise CNC machining and grinding is typically used in the production of Menatek's critical components.
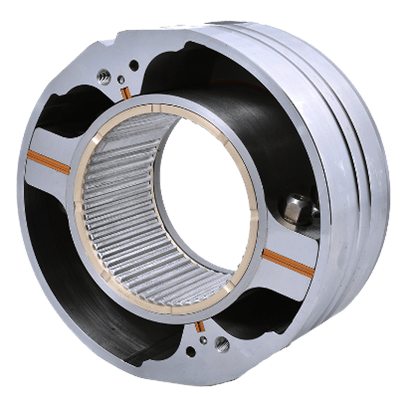
Gear manufacturing refers to the process of fabricating gears, which are mechanical components that transmit power and motion between machines. The quality of a gear refers to its ability to transmit power and motion smoothly and accurately. It is typically indicated by a standard such as the DIN 4 standard in Europe.
Gears of Menatek that meet the DIN 4 quality standard are considered to be of high quality and suitable for use in critical applications. To manufacture gears that meet this standard, Menatek typically use advanced equipment and techniques to ensure that the gears are fabricated to precise specifications. Other techniques such as heat treatment and grinding may also be used by Menatek to improve the quality of the gears.
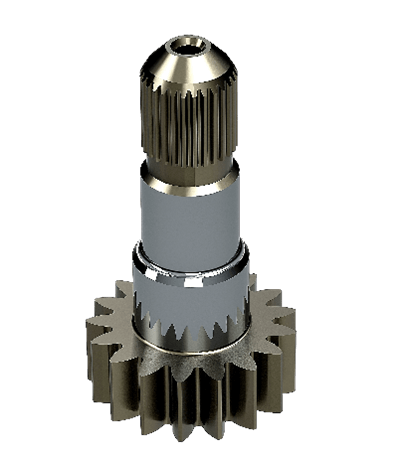
Forging is a manufacturing process in which metal is shaped by hammering, pressing, or rolling. Menatek's forging capabilities include open die forging, closed die forging, and ring rolling. Open die forging is typically used to create large, custom-shaped parts, while closed die forging is commonly used to create small, high-precision parts. Ring rolling is often used to create parts for build to print capabilities of Menatek. Aluminum can be forged using any of these processes, depending on the size, shape, and precision of the requested part and the priorities of Menatek's key partners.

Cold forming is a manufacturing process in which metal is shaped at room temperature using tools and dies. Menatek has several cold forming techniques, including deep drawing and flow forming. Deep drawing is often used to create complex-shaped parts, while flow forming is often used to create lightweight, high-strength parts. Both deep drawing and flow forming have several advantages over other manufacturing processes, including the ability to create complex shapes with high accuracy, a good surface finish, and minimal waste. They are also often faster and more cost-effective than processes such as forging or machining.

One of the biggest challenges faced by Original Equipment Manufacturers (OEMs) is the delivery of maintenance parts in a timely manner, which can extend delivery dates and delay operational readiness. Menatek, on the other hand, owns the biggest supply chain in Türkiye, which enables the company to run a fast-paced approach and ensure a high state of readiness.
In summary, Menatek Defense Technologies offers specialized expertise in manufacturing subsystems of heavy to light military vehicles. The company's comprehensive manufacturing capabilities, skilled team, and in-house testing capabilities enable it to deliver high-tech components and products that meet the highest quality standards while ensuring a high state of readiness for its clients. With its dedicated focus on designing and delivering innovative solutions, Menatek has established a reputation as a reliable partner for military vehicles and high-tech industries.